Manganese steel, also called Hadfield steel or mangalloy, is to improve STRENGTH , DURABILITY & TOUGHNESS, which is the strength of ais the most common material for crusher wears. All round manganese level and the most common for all applications is 13%, 18% and 22%.
But do you know, what’s the different among them?
Here we’ll introduce the main different manganese for you simply.
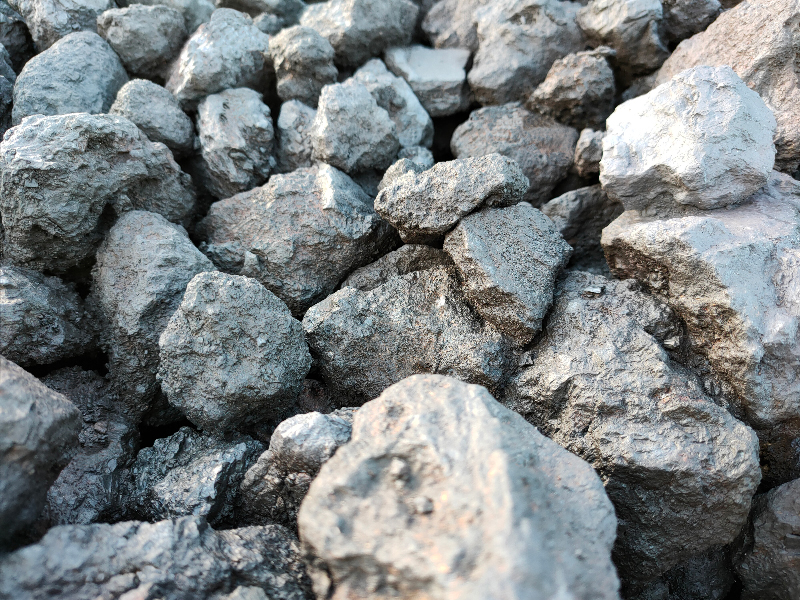
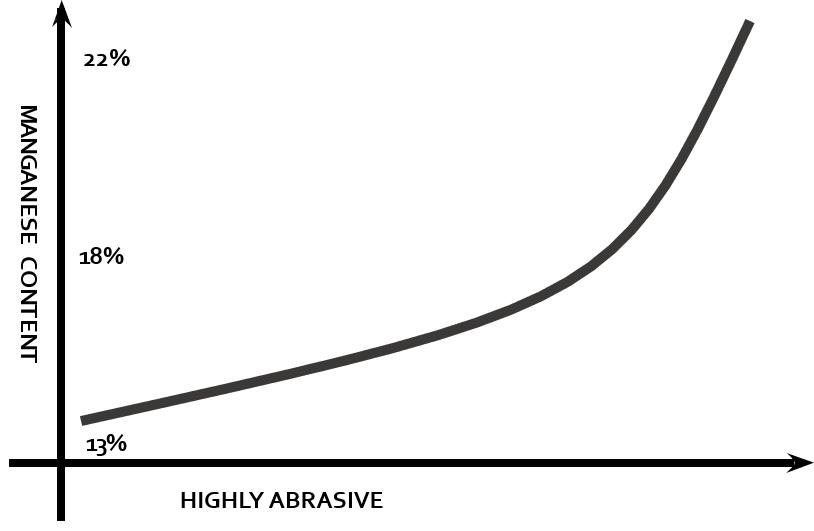
1、13% MANGANESE
The Standard of this 12-14 % Manganese includes. It’s available for use in soft low abrasion applications, especially for medium & non-abrasive rock, and soft & non-abrasive materials.
The main feature of this product is its high wear and resistance
Severe wear on the surface has a work-hardening effect on the austenitic structure of this steel. When combined with the level of carbon in accordance with the international standards, leads to increase hardness from 200BHN (in as delivered plate) up to an in-service hardness of at least 600BHN.
This work-hardening capability renews itself throughout in-service life. The under layers not work-hardened maintain an excellent resistance to shock and a very high ductility.
2、18% MANGANESE
18% manganese wear parts are middle-of-the-road. It’s standard fit for all Jaw & Cone crushers. Almost suitable for all rock type, but not fit for hard & abrasive materials.
3、22% MANGANESE
An option available for all Jaw & Cone crushers.
Especially work hardens quick in abrasive applications, better suitable for hard & (non-) abrasive, and medium & abrasive materials. 22-24% manganese wear parts represent the high end of the spectrum. At this level of manganese, wear parts are brittle, and so they’re only suited for high abrasion material that’s even more brittle.
Anyway, Choosing the Right Manganese Wear Parts always is your best crushing solution.
If you need any supports, we are always available.
Post time: Jul-26-2023