Are you guilty of wasteful wear on your jaw crusher liners?
What if I had to tell you that you can improve profitability by studying your old, worn jaw crusher liners?
It is not unusual to hear about a liner’s wasteful wear when it has to be replaced prematurely. Production dips, product shape changes and this CAN lead to critical failures on your jaw crusher.
By the time you notice this, it is very difficult to pinpoint the cause. Tracing a jaw crusher’s liner wear over its normal wear life is important, as it effects the machines overall performance, product shape, size and production throughput. Three major factors play a role in wasteful wear. Casting quality, process flow and material properties.
Casting related:
If the material integrity is in doubt from the customer, it could only be resolved if a sample is removed from the liner and a chemical analysis is done. Some of these liners do not come with a batch casting number like a Metso OEM liner; traceability is not possible and it will be very difficult to investigate and rectify the problem.
Process related:
When a liner wears abnormally in the middle or more than at the bottom, it indicates that a majority of single sized oversize material is being fed into the crushing chamber. This could also be the product of grizzly bars being spaced too far apart and by-passing finer feed materials from the jaw crusher chamber or an uneven graded mix of coarse and finer material are being fed into the jaw crusher crushing chamber.
Intermittent feed into a jaw crusher chamber can lead to a liner crushing in the middle of the cavity leading to crushing only at the bottom end of the crushing zone.
Looking at the erratic wear on corners of the liner, circled and pointed out in blue. Understanding this odd wear pattern can lead us to another possible process related issue which has to do with the jaw crusher’s discharge chute design.
We should also consider moisture being introduced to material in the form of the dust suppression system. Moisture being added to feed material increases the wear exponentially to wear parts. Dust suppression should be strategically placed to supress dust, not to impact the abrasiveness of the material.
Material properties:
Lastly we know that material properties vary from location to location in the same pit where it is mined from. Silica content varies and is not constant. The previous set might have seen material from one side of the quarry pit and the wasteful wear might have been from material from another side of the quarry pit. This needs to be investigated.
Spending time on site looking at the process flow will reveal possible factors that leads to wasteful wear. It might be a time consuming investigation, but can lead to huge financial yields.
Don’t become a victim of wasteful wear and believe that your operation is perfect without taking the effort to study these worn liners.
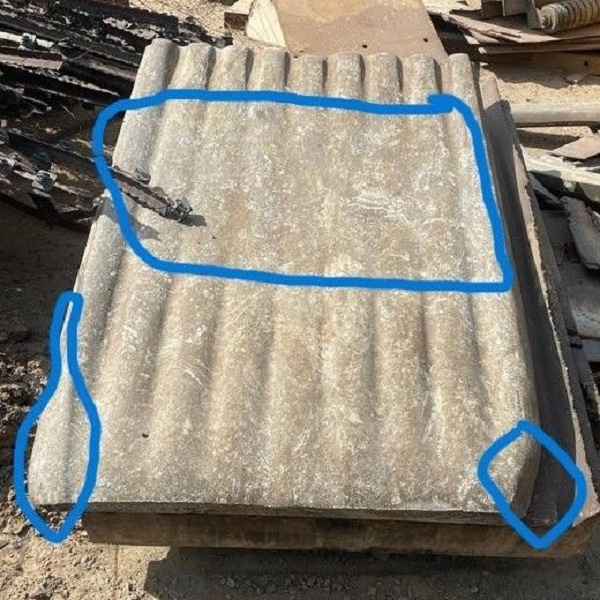
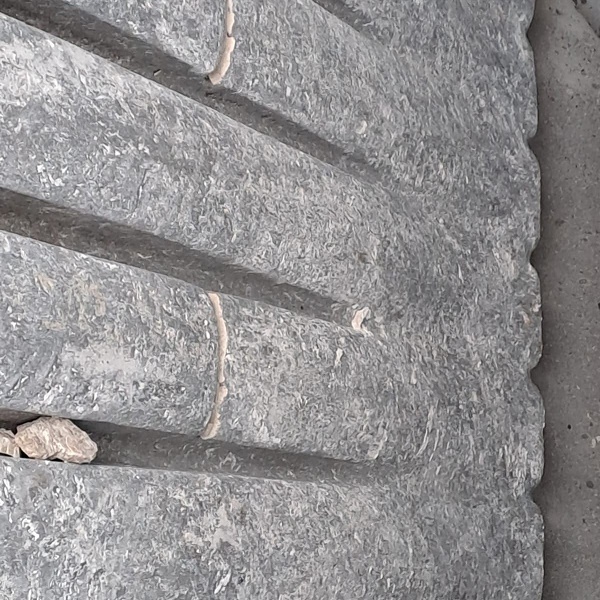
By Charl Marais
News From https://www.linkedin.com/feed/update/urn:li:activity:7100084154817519616/
Post time: Sep-14-2023